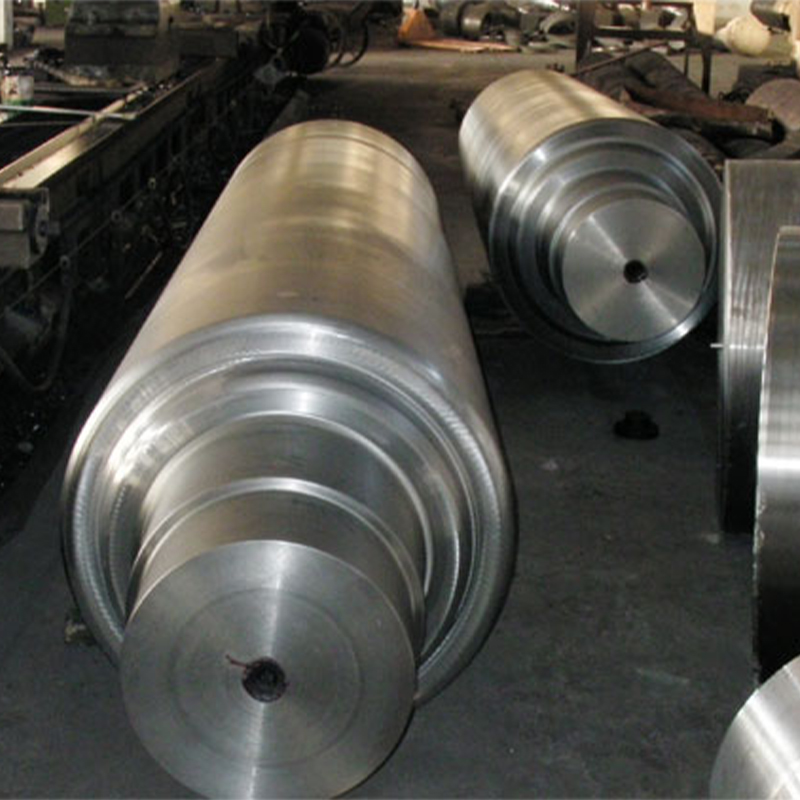
Alloy Round Bars should be stored in an environment that offers protection from atmospheric moisture, dust, and pollutants, as these factors significantly contribute to oxidation and surface degradation. Indoor storage areas are preferred over outdoor locations to avoid direct exposure to rain, dew, and UV radiation, which can accelerate corrosion and material fatigue. The storage space should be climate-controlled, maintaining relative humidity levels ideally below 60% to prevent the formation of condensation on the metal surfaces. Temperature stability is equally important to avoid thermal cycling that may cause moisture buildup through condensation. Good ventilation facilitates air circulation, which helps disperse moisture and prevents stagnant humid pockets around stored bars. For facilities without advanced climate control, dehumidifiers and air purifiers can be installed to further reduce corrosion risk.
Direct contact with the ground or with incompatible materials can introduce contaminants or physical damage to Alloy Round Bars. Using wooden, plastic, or metal racks designed to distribute weight evenly reduces localized stress points and deformation risk, especially for heavier or longer bars. Bars should be separated by non-abrasive materials such as rubber pads, felt, or coated spacers to prevent scratching or abrasion during stacking and movement. The height of stacked bars must be controlled to avoid excessive load on lower layers, which can cause permanent deformation or bending. Careful segregation of different alloy grades prevents cross-contamination and chemical interaction that might trigger galvanic corrosion. Storage areas must be kept clean and free from spills of oils, chemicals, or cleaning agents that could react adversely with the metal surface or protective coatings.
For alloy grades prone to oxidation or when storage exceeds several weeks or months, applying a temporary protective coating is advisable. These coatings include corrosion inhibiting oils, greases, waxes, or specialized anti-rust sprays formulated for metal surfaces. Such barriers prevent oxygen and moisture from contacting the alloy surface, slowing oxidation reactions. The choice of coating should consider ease of removal to ensure no residues interfere with subsequent machining, welding, or finishing processes. In addition to coatings, wrapping Alloy Round Bars in corrosion-resistant packaging materials like polyethylene film, VCI (volatile corrosion inhibitor) paper, or plastic sheeting enhances protection against humidity and airborne contaminants. These wrappings should be sealed adequately to create a moisture barrier but also allow periodic inspection without complete unwrapping.
Mechanical damage such as dents, scratches, or deformation can significantly compromise the surface integrity and may initiate localized corrosion or stress concentrations. Using lifting equipment equipped with padded slings, soft hooks, or clamps lined with rubber or nylon prevents direct metal-to-metal contact during movement. Forklift tines or crane hooks should be handled with care to avoid gouging or surface indentation. Manual handling requires personnel to wear clean gloves to minimize contamination from skin oils, salts, or dirt, which can accelerate corrosion or stain surfaces. Avoid dragging Alloy Round Bars over rough surfaces or against other bars, as friction can remove protective coatings and create micro-abrasions. Training staff on proper handling procedures helps maintain product quality and safety.
Implementing a systematic inventory rotation such as First-In, First-Out (FIFO) prevents prolonged storage of materials, thereby minimizing the duration of exposure to potentially harmful environments. Scheduled inspections at regular intervals should assess the condition of stored Alloy Round Bars, checking for signs of surface discoloration, rust spots, pitting, or physical deformation. Early detection enables timely intervention through cleaning, re-application of protective coatings, or segregation of damaged stock to prevent spread. Inspection records support quality control, facilitating compliance audits and traceability in regulated industries. Effective inventory management also ensures that materials are readily available for timely processing, reducing lead times and production disruptions.